Damage Control Measures in Composites: Focus on Damage Tolerance of Aerospace Structures
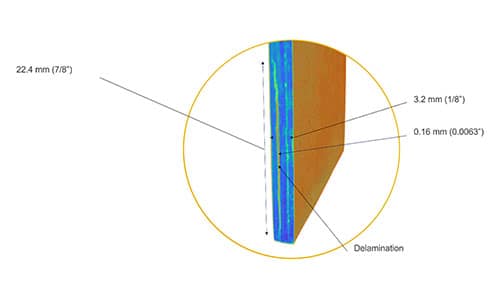
Damage control in composites has become one of the major topics of research, as primary structures are transitioning to composites for the benefits of their lightweight, ease of manufacturability and high strength-to-weight ratio. However, one of the significant challenges with composites is that there is still no accepted standard to define the damage and its propagation compared to well-studied metallic structures. The main objective of this proposal is immerse academia into a systematic study to synergistically contribute to structural integrity of composite structures. The proposed research will follow the main guidelines of national Agencies with the initiative to create an efficient simulation-based approach to predict the potential initiation of damage propagation in a composite structure, based on well controlled and monitored test results. The predictive analysis will incorporate a physics-based methodology for assessing irreversible deformation. The objective is to introduce and calibrate a model that follows the micromechanical of the deformed composite material system. By inducing initial beyond visual impact damage (BVID) in coupons made under industrial standard, the propagation and integrity of the components will be evaluated under different levels of load and loading modes to establish an acceptable standard for fracture control measures in composite laminates.
Main investigator: Kais Jribi, Ph.D. Candidate
Digital Image Correlation of ZnO-Modified Fiber-Matrix Interface
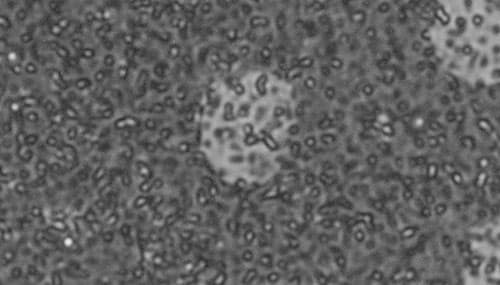
Use of composites in aerospace primary structures has become frequent for well-known benefits, including high strength to weight ratio. Improving the fiber-matrix interface adherence is one important step for expanding the use of composites. Work has been performed in modifying carbon fibers by growing zinc oxide (ZnO) nanorods in the fiber surface using a hydrothermal approach, increasing interfacial area and fiber-matrix friction. Macroscale evaluation has shown that the interfacial modification decreases the inter-ply movement and reduces the processing strains and residual stresses. To fully understand the mechanism taking place at the interface, a microscale evaluation must be conducted to determine the fiber-matrix interaction analyzing the thermal behavior and cure kinetics due to increase fiber surface area, and improved strength due to increase in interface friction. The proposed approach is to use HD Scanning Electron Microscope (SEM) digital image correlation (DIC) for mapping the interface by using speckles in nanoscale. The speckle pattern will be created with Ti nanopowder for strain maps in the fiber-matrix interface. The main objective of this research is to develop a protocol for speckling the modified single fiber composite and show that DIC can be used in microscopic level to evaluate the fiber-matrix interface behavior for future SEM in-situ experiments.
Main investigator: James Harris, Master’s Candidate
Probabilistic Damage Tolerance Analysis
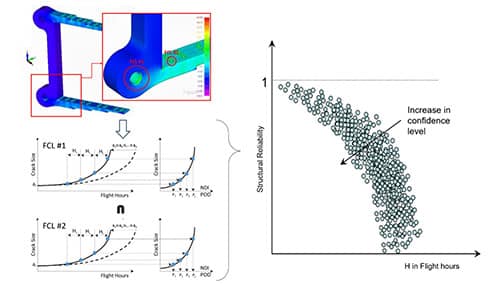
Aerospace structures are subjected to cyclic loads that can lead any initial undetected defect to a catastrophic failure. Ideally, any fracture control plan should be based on the acceptable probability of failure. The traditional fracture control measures for aircraft structures contemplate damage tolerance analysis (DTA), which define inspection intervals that would guarantee structural integrity. In this methodology, all the parameters, material properties, loads and operational environment are considered to be deterministic. The uncertainty is introduced to the non-destructive inspection (NDI) intervals by considering a scatter factor at the end of the process. Sometimes, the cumulative probability of detection can also be included, and then the process can be adjusted to meet the Federal Aviation Administration (FAA) (or equivalent military) risk assessment. However, not only field inspection but material properties, initial quality, loads and environment are subjected to variability, which can deeply impact the structural reliability and airworthiness condition of an aircraft structure. Another aspect not covered by the traditional DTA is the multiple site damage in the same primary structure. This is not to be confused with wide-spread fatigue damage, which is the hypothesis that each initiation site is considered to interact with each other during a determinist analysis. The multiple site damage will include another uncertainty in the analysis, which would be the impact of the probability of one, any or all the fatigue critical locations (FCL) reaching a critical crack size.
Main investigator Breno De Bruns, Master’s Candidate
The Role of Slip System Activations on Ni-Based Superalloy High-Temperature Fatigue Life
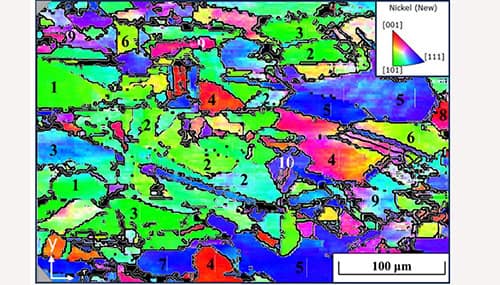
Ni-based superalloys are widely used in turbine engines mainly due to their high strength and fatigue resistance at elevated temperatures. A hypothesis to explain its atypical characteristic among metals is that a cross-slip mechanism is in place. The activation of {100} cubic slip systems along of the octahedral slip planes {111} in Ni-based superalloys has been verified when under high strain and temperature. The material would exhibit a more homogeneous strain distribution and less strain localization. In previous research, it was observed that preconditioning of the material improved the fatigue life of the sample. The preconditioning involved applying a 1% strain to the material at 700°C, then fatigue it at 500°C under operational cyclic loading. We plan to use the Scanning Electron Microscope to observe the slip planes before and after conditioning to be able to determine if a change in the material's microstructure is what leads to the improvement of the sample's fatigue life. With a focus on the deformation mechanism, the sample microstructure will be fully characterized by electron backscatter diffraction (EBSD) and the slip systems, after the applied pre-condition, will be tracked via digital image correlation (DIC).
Main investigators: Alexandru Lopazan, MSc; Paulina Estefania De La Torre, MSc
Effect of Fatigue and Galvanic Corrosion on Cold Expanded Holes in Aluminum Alloys
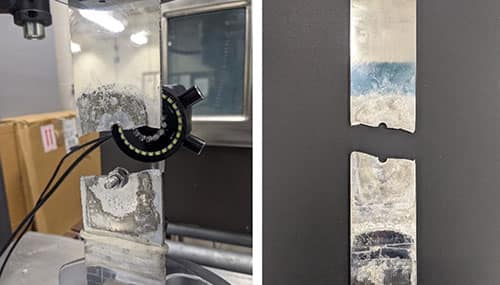
This study evaluated the effect of pre-cracks on residual stress distribution of coldworked holes and the impact on the stress intensity factors. For its completion, AA2024-T3 samples were dimensioned and manufactured following best practices and results from classic plasticity theories. Analytical stress and strain calculations were compared to numerical solutions from elastic-plastic analysis using NX Nastran FEMAP, as well as experimental strain measurements calculated by calibrated digital image correlation with the use of images taken during the cold-working process. The fatigue life was compared between pre-cracked open and cold expanded specimens. The crack growth was monitored using a digital microscope. Then, the research established the effect of hole cold expansion on the fatigue life of pre-cracked material under aggressive environment. A relationship between crack propagation and secondary crack initiation was established for AA2024-T3 cold-worked holes subjected to cyclic loads to determine the impact on the fatigue life of joints in the presence of saline solution. Galvanic corrosion of a steel fastener/aluminum plate assembly was investigated in the presence of cracks in the aluminum plates, whose growth was monitored in-situ with a digital microscope throughout the fatigue process.
Main investigators: Ken Shishino, MSc; Christopher Leirer, MSc
Seaplane Design Analysis: Hull Optimization for Water Suppression
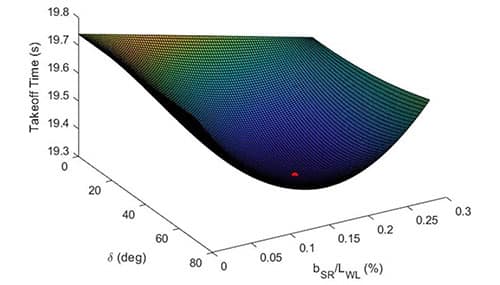
Amphibian aircraft have seen a rise in popularity in the recreational and utility sectors due to their ability to take off and land on both land and water, thus serving a myriad of purposes, such as aerobatics, surveillance and firefighting. Such seaplanes must be aerodynamically and hydrodynamically efficient, particularly during the takeoff phase. Naval architects have long employed innovative techniques to optimize the performance of marine vessels, including incorporating spray rails on hulls. This research paper is dedicated to a comprehensive investigation into the potential utilization of spray rails to enhance the takeoff performance of amphibian aircraft. Several spray rail configurations obtained from naval research were simulated on a bare Seamax M22 amphibian hull to observe an approximate 10-25% decrease in water resistance at high speeds alongside a 3% reduction in the takeoff time. This study serves as a motivation to improve the design of the reference airplane hull and a platform for detailed investigations in the future to improve modern amphibian design.
Main investigator: Soham Bahulekar, MSc
Stress Intensity Factor Via Finite Element Modeling (FEM) and Asymptotical Solution
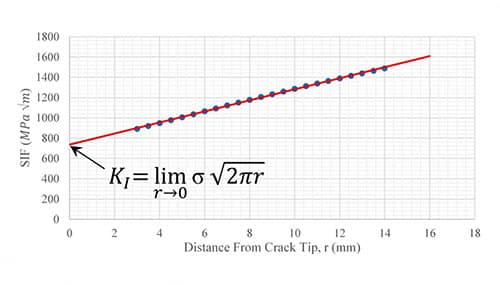
This research explored the modeling of a cracked structure using a linear elastic finite element method (FEM) analysis with the objective of determining the stress intensity factor (SIF) for complex geometries. The analysis uses a mapping of the stress concentration area ahead of the crack tip to asymptotically determine the SIF. For model calibration, Irwin’s approximation method was used in two known crack case solutions subjected to a uniform tensile loading (Mode I – Opening) with fixed geometric dimensions. With a focus on aircraft airworthiness application, two more complex geometries with irregular stress distributions were analyzed and the results were extracted for future use in crack growth simulation.
Main investigator: Hamid A Ghassri, B.S.
Failure Analysis of Aluminum Alloy Subjected to Cyclic Load and Aggressive Environment
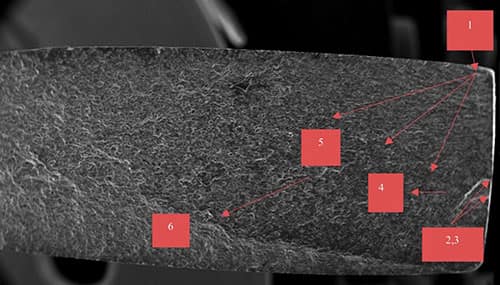
In previous research within this group, four nearly identical samples of AA2024-T3 were prepared and tested under varying conditions (control, with cold work, with cold work and corrosive environment) to understand how the material would be affected. Two of these specimens reacted in an unanticipated manner. This research aimed to determine the cause of the unanticipated behavior observed. The sample was cut to a smaller size and observed using a Scanning Electron Microscope (SEM) and analyzed using Energy-Dispersive X-ray Spectrometry (EDX). The analysis revealed the presence of Cu-based precipitates which caused pitting in the surface of the specimen. This pitting initiated a crack away from the center of the specimen which eventually caused the ultimate failure of the specimen in an unexpected area. Routine inspections are recommended due to this conclusion as a method to reduce failure in structures and parts exposed to aggressive or corrosive environments.
Main investigator: Brian Wier, B.S
NSF-REU Site: Exploring Aerospace Research at the Intersection of Mechanics, Materials Science and Aerospace Physiology
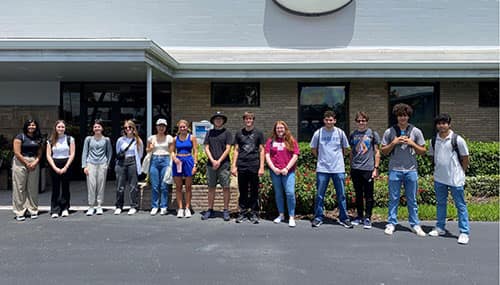
This project aims to educate students and promote scientific research in materials and aerospace science that encompasses not only building lighter and smarter materials for aerospace applications but also understanding the impact of the space environment on physiological and biological changes. This site focuses on multidisciplinary research in aerospace engineering, chemistry and applied space biology, with a goal of improving future space materials science and human diagnostic technology by exposing students to the challenges in these areas and the research going on to solve them. Undergraduate students for a 10-week summer research were recruited for the 2022 and 2023 summer programs. New students will be selected for summer 2024. The student recruitment starts in November of each year, and the final selection based on mentors and diversity criteria is taken in April.
Sponsor: NSF Grant #2050887; PI: Prof. Foram Madiyar (COAS), Co-PI: Prof. Alberto Mello